Isomerization is a chemical process in which a molecule undergoes a rearrangement of its atoms, resulting in the formation of a different isomer.
Isomers are molecules that have the same molecular formula but different structural arrangements of their atoms.
Isomerization can occur spontaneously or can be induced by external factors such as heat, light, or the presence of a catalyst.
This process is important in organic chemistry, where isomerization reactions are widely used to create new compounds or to convert one compound into another with specific properties.
Isomerization reactions can involve different types of isomers, such as structural isomers, stereoisomers, or geometric isomers.
The resulting isomer can have different physical and chemical properties, such as melting point, boiling point, reactivity, and biological activity.
What is isomerization in oil refining?
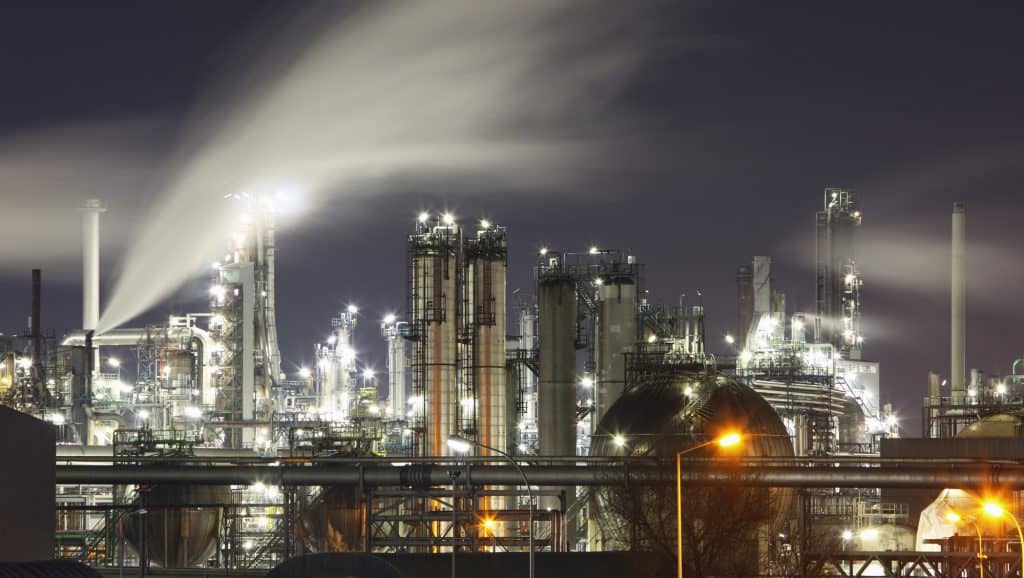
Isomerization is a process used in oil refining to convert straight-chain hydrocarbons into branched-chain hydrocarbons, which have higher octane ratings and better performance characteristics as gasoline components.
The process typically involves the use of a catalyst, such as platinum or zeolite, under high pressure and temperature conditions.
The isomerization process is particularly useful in the refining of light naphtha, a gasoline blending component obtained from crude oil or natural gas.
Light naphtha typically contains a high percentage of straight-chain hydrocarbons, which have low octane ratings and can cause engine knocking.
By converting these hydrocarbons into branched-chain isomers, the resulting gasoline blendstock has a higher octane rating and can be used in high-performance engines without causing knocking.
Isomerization is a key process in the production of reformulated gasoline, which is required by environmental regulations in many countries.
Reformulated gasoline contains lower levels of harmful pollutants such as benzene and has better air quality performance.
The isomerization process is also used in the production of other high-value products, such as jet fuel and petrochemical feedstocks.
What is the difference between straight-chained and branch-chained hydrocarbons?
Straight-chained hydrocarbons are hydrocarbon molecules that have a linear or straight-chain arrangement of carbon atoms.
In other words, the carbon atoms are connected to each other in a single, unbranched chain. An example of a straight-chain hydrocarbon is n-butane (C4H10), which has a four-carbon chain.
On the other hand, branched-chain hydrocarbons are hydrocarbon molecules that have one or more branches or side chains attached to the main chain of carbon atoms.
These side chains can be either methyl (-CH3) or ethyl (-CH2CH3) groups. An example of a branched-chain hydrocarbon is isobutane (C4H10), which has a three-carbon chain with a methyl group attached to the second carbon atom.
The main difference between straight-chained and branched-chain hydrocarbons is their physical and chemical properties.
Branched-chain hydrocarbons have higher octane ratings and burn more efficiently in gasoline engines, which makes them more desirable as gasoline components.
This is because the branched chains disrupt the ability of the hydrocarbon molecules to pack closely together, which reduces the likelihood of premature ignition and engine knock.
Additionally, branched-chain hydrocarbons have lower boiling points and lower melting points than straight-chain hydrocarbons, which affects their behavior in different conditions.
Straight-chain hydrocarbons tend to have higher viscosity, higher melting points, and higher boiling points than branched-chain hydrocarbons.
Where does isomerization occur in a refinery?
Isomerization typically occurs in a dedicated isomerization unit within an oil refinery. The unit is designed to process light naphtha feedstock, which is a low-octane gasoline blending component produced from crude oil or natural gas.
The isomerization unit typically consists of several stages, including a pre-treatment stage, a reactor stage, and a product separation and purification stage.
In the pre-treatment stage, the feedstock is treated to remove impurities such as sulfur, nitrogen, and oxygen compounds, which can deactivate the catalyst used in the isomerization process.
In the reactor stage, the pre-treated feedstock is passed through a catalyst bed, where the straight-chain hydrocarbons are converted into branched-chain isomers. The catalyst used in the isomerization process is typically a metal such as platinum or palladium supported on a porous material such as zeolite.
The product separation and purification stage involves separating the isomerized product from unreacted feedstock and other by-products such as hydrogen gas.
The separated product is then sent to further processing units or blended with other gasoline components to produce finished gasoline.
Isomerization units are typically located in the gasoline production area of the refinery, which is responsible for producing gasoline blending components and finished gasoline products.
The isomerization process is an important step in producing high-octane gasoline components that meet regulatory requirements for cleaner burning and better engine performance.
Related Resources
Energy Risk Management
Risk Management in Oil and Gas
Oil 101
Power 101
What is a Nuclear Power Reactor Operator
Watts, Kilowatts, Megawatts, Gigawatts
Jobs Data
Global Energy Talent Index (GETI)
US Energy & Employment and Jobs Report (USEER)
Career Path in Energy Articles
Is Oilfield Services/Equipment a Good Career Path
Is Oil and Gas Production a Good Career Path
Is Electric Utilities a Good Career Path
Is Power Generation a Good Career Path