Fractional distillation is a separation process used to separate a mixture of two or more liquids with different boiling points. The process involves heating the mixture to vaporize the liquid with the lowest boiling point, which is then condensed and collected as a separate liquid.
The remaining mixture is then heated to vaporize the next liquid with the higher boiling point, which is also condensed and collected as a separate liquid. This process is repeated until all of the liquids in the mixture have been separated.
The key to fractional distillation is the use of a fractionating column, which is a long tube packed with a material that provides a large surface area for the vapor to condense on. As the vapor rises through the column, it comes into contact with the packing material, which causes some of it to condense back into liquid form.
The liquid then flows back down the column, where it is re-vaporized and re-condensed again and again until it reaches the point in the column where its boiling point matches the temperature of the column. At this point, the liquid can pass through the column as a pure distillate.
Fractional distillation is a widely used technique in the chemical and petroleum industries for separating and purifying different components of crude oil, as well as in the production of various chemicals and fuels.
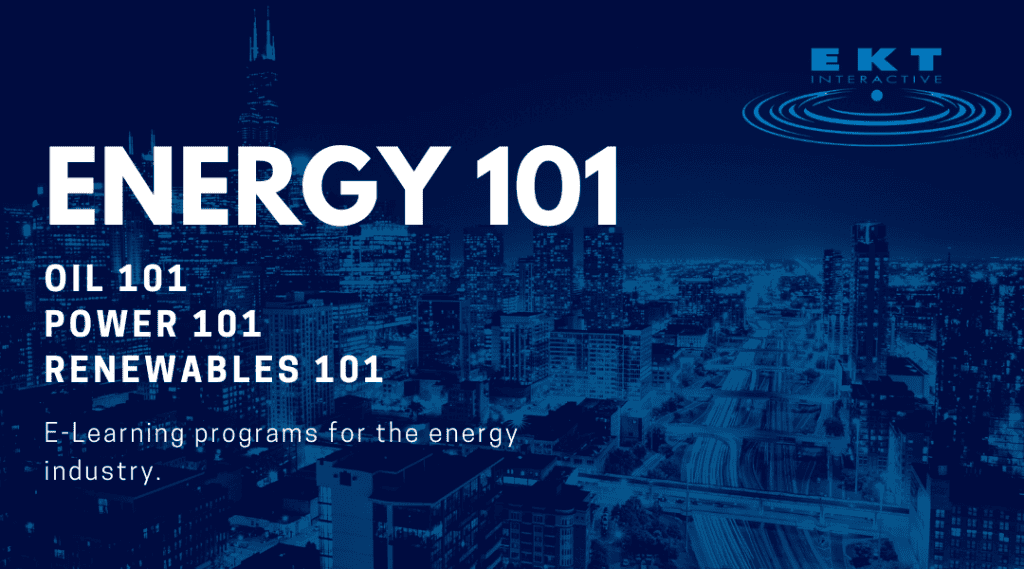
Whether it’s oil and gas, power, or renewables that is your chosen career path, our e-learning courses can help you get a leg up on the competition and get your food in the door.
We often hear from learners who successfully use our courses to prepare for the interview process. After all, you’re using the same courses that companies themselves use to prepare their teams.
As this student passed on:
I would like to thank you for your brilliant Oil 101 materials. I did use it to prepare for the recruitment process, and managed to take a new role in the oil and gas industry!
Get started with our Energy 101 courses today!
How does fractional distillation work?
Fractional distillation is a separation process that works on the principle that liquids with different boiling points will boil at different temperatures. Here is a step-by-step explanation of how fractional distillation works:
- A mixture of two or more liquids with different boiling points is placed in a distillation flask.
- The distillation flask is connected to a fractionating column, which is a long tube filled with a packing material that provides a large surface area for the vapor to condense on.
- The mixture is heated, usually using a heat source such as a Bunsen burner or an electric heating mantle. The liquid with the lowest boiling point begins to vaporize first.
- The vapor rises up the fractionating column and comes into contact with the packing material. The packing material provides a large surface area for the vapor to condense on, which causes some of the vapor to turn back into liquid form.
- As the vapor continues to rise up the column, it undergoes repeated cycles of vaporization and condensation. This causes the vapor to become enriched in the component with the lowest boiling point.
- When the vapor reaches the top of the fractionating column, it passes through a condenser, which is a coiled tube cooled by running water. The vapor condenses back into a liquid and is collected in a separate flask.
- The remaining liquid in the distillation flask is then heated further, causing the liquid with the next lowest boiling point to vaporize and repeat the process. This continues until all of the liquids in the mixture have been separated.
- The collected fractions can then be analyzed and further purified if necessary.
Fractional distillation is a powerful tool for separating and purifying liquids with different boiling points.
It is widely used in the chemical, pharmaceutical, and petroleum industries for the separation of various chemicals and fuels.
Is fractional distillation part of the refining process?
Yes, fractional distillation is a key part of the refining process in the petroleum industry. Crude oil is a mixture of hydrocarbons with different boiling points, ranging from light gases such as methane and propane to heavy liquids such as bitumen.
To separate and purify these different hydrocarbons, crude oil is subjected to fractional distillation, which separates the hydrocarbons into fractions based on their boiling points.
In a petroleum refinery, crude oil is first heated and then introduced into a distillation tower or column, which is a tall vertical vessel with trays or packing material. As the crude oil is heated, it vaporizes and rises up the column.
The packing material provides a large surface area for the vapor to condense on, which causes some of the vapor to turn back into liquid form. This process of vaporization and condensation causes the different hydrocarbons in the crude oil to separate into different fractions based on their boiling points.
The lightest hydrocarbons, such as methane and propane, have the lowest boiling points and are separated at the top of the column. As the temperature in the column decreases with height, heavier hydrocarbons condense and are collected on trays or at different heights in the column.
The heaviest hydrocarbons, such as bitumen, have the highest boiling points and are collected at the bottom of the column.
The separated fractions are then further processed through other refining processes such as cracking, reforming, and treating to produce different products such as gasoline, diesel fuel, jet fuel, and various petrochemicals.
What is a boiling point in refining?
In refining, boiling point is a critical property of hydrocarbons. Boiling point is the temperature at which a liquid changes into a gas (vapor) at a given pressure. In refining, boiling point is used to classify hydrocarbons into different fractions during fractional distillation.
Crude oil is a mixture of hydrocarbons with different boiling points, ranging from light gases such as methane and propane to heavy liquids such as bitumen.
During fractional distillation, crude oil is heated in a distillation tower or column, and the hydrocarbons are separated into different fractions based on their boiling points.
The lightest hydrocarbons, such as methane and propane, have the lowest boiling points and are separated at the top of the column. As the temperature in the column decreases with height, heavier hydrocarbons condense and are collected at different heights in the column.
The heaviest hydrocarbons, such as bitumen, have the highest boiling points and are collected at the bottom of the column.
Boiling point is also used to determine the properties and potential uses of different refined products.
For example, gasoline is typically composed of hydrocarbons with boiling points ranging from about 30°C to 220°C, while diesel fuel is composed of hydrocarbons with boiling points ranging from about 180°C to 360°C.
The boiling point range of a refined product determines its volatility, or tendency to evaporate, which affects its use as a fuel.
Overall, boiling point is a key property of hydrocarbons in refining, and is used to classify and separate them into different fractions based on their physical properties, potential uses, and economic value.
What equipment is used in fractional distillation?
Fractional distillation is a separation process that requires specific equipment to carry out. The equipment used in fractional distillation includes:
- Distillation flask: This is a round-bottomed flask that holds the mixture of liquids to be separated.
- Fractionating column: This is a long vertical column that is packed with a material that provides a large surface area for the vapor to condense on. The packing material can be glass beads, ceramic rings, or other materials. The column is typically insulated to prevent heat loss.
- Heat source: This can be a Bunsen burner, an electric heating mantle, or other heating devices that can provide a controlled source of heat.
- Condenser: This is a coiled tube or a series of tubes that are cooled by running water. The condenser is used to cool and condense the vapor as it rises up the fractionating column.
- Collection flasks: These are separate flasks or containers used to collect the different fractions of the separated liquids.
- Thermometer: This is used to monitor the temperature of the vapor as it rises up the fractionating column.
- Vacuum pump (optional): In some cases, a vacuum pump may be used to lower the pressure inside the fractionating column. This can be useful for separating liquids with very high boiling points or for reducing the risk of thermal decomposition.
Overall, the equipment used in fractional distillation is designed to heat, separate, and collect different fractions of a mixture of liquids with different boiling points.
The use of specialized equipment and careful control of operating conditions are critical to achieving a successful separation.
Related Resources
Energy Risk Management
Risk Management in Oil and Gas
Oil 101
Power 101
What is a Nuclear Power Reactor Operator
Watts, Kilowatts, Megawatts, Gigawatts
Jobs Data
Global Energy Talent Index (GETI)
US Energy & Employment and Jobs Report (USEER)
Career Path in Energy Articles
Is Oilfield Services/Equipment a Good Career Path
Is Oil and Gas Production a Good Career Path
Is Electric Utilities a Good Career Path
Is Power Generation a Good Career Path