Thermal power plants utilize heat from a fuel source and specific types of equipment to produce electricity, generally in three-steps:
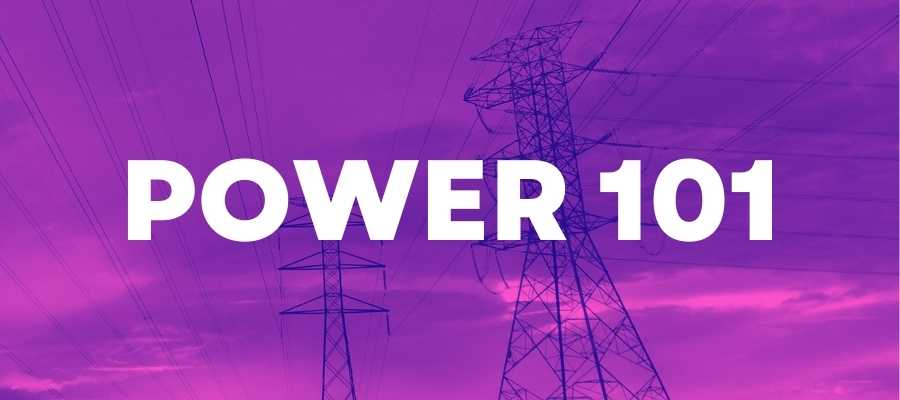
Power 101 – How the global power sector works
First, coal or oil is burned to heat water, converting it to steam.
The collected pressurized steam is directed to power a steam turbine.
And finally, energy created by the turbine drives a generator that produces electricity.
It is a common misconception that gas-fired power plants also operate in this way.
This is not the case and their operation will be described in more detail in our module entitled Natural Gas-Fired Power Plants.
For now we will only focus on coal and oil-fired thermal power plants.
The Thermal Power Plant
Learn more with our Energy 101 online course series. Energy 101 covers everything from oil and gas to power and renewables and is used by companies and individuals around the world.
The Basics of Steam in Thermal Power
It all begins with water.
The water molecule is comprised of three atoms, two-hydrogen and one-oxygen. Like all molecules, it’s always in a state of motion.
When heat is applied, its movement increases in relation to its temperature. If the temperature is raised, will the molecule move faster or slower? Faster, of course.
The boiling point is where water is converted from a liquid state to a gas state.
Boiling point temperature is a function of the pressure surrounding the water. At atmospheric pressure of 14.5 psi, boiling occurs at 100 degrees Celsius or 212 degrees Fahrenheit.
As more heat is applied, the water evaporates at an exponential rate thus creating steam.
Steam Vocabulary
Some steam vocabulary is needed to understand power plant operations.
Saturated Steam, called dry steam, occurs at temperatures and pressures where steam (a gas) and water (a liquid) can coexist, like 100°C, at atmospheric pressure.
In early boilers, only one third of the heat in the fuel was initially turned into power.
Boilermakers developed various designs to squeeze the most energy out of the fuel, and to maximize heat transfer to the water.
Today, a common boiler design uses saturated steam with a temperature of 335° C in a 2,000 psi boiler drum.
Unsaturated steam, called wet steam, is the most common form of steam generated in the power plant boiler.
Wet steam contains non-vaporized water molecules. Even the best boilers today may discharge steam that is still 3 – 5% wet.
Superheated steam is needed and created by further heating wet steam beyond the saturated steam point.
By putting wet steam through a superheater the temperature is raised to 500° C.
In the superheater, the temperature of the steam goes up, but the pressure does not.
The Boiler
Let’s start with the main power plant component used to produce steam – the boiler.
In its basic form, a boiler is not much different than a kettle.
Like a kettle, a heat source raises the water temperature inside the boiler, turning it into steam which forms a high pressure.
Early boilers were simply single-cavity metal vessels that held water, which was heated by a firebox to produce steam. This design limited steam energy to the pressure that the vessel outer wall, called a shell, could contain.
After James Watt developed the steam engine in 1775, the machinery, ships, and locomotives that used steam propulsion required much more power.
To increase steam producing power, more of the heat from the fuel had to be transferred to the water, while maintaining control of the resulting pressurized steam.
To accomplish this, engineers designed boilers that conveyed the feedwater in metal water-tubes surrounded by the fuel burner heat.
Because the water-tubes have a small internal surface area, this design produces higher steam pressures that can be safely controlled.
This new design also reduced the shell wall thickness needed for the boiler drum to operate safely.
For our purposes, a boiler is now defined as an enclosed container, with internal tubes, using thermal energy to convert water into pressurized steam with the intent of creating electricity.
Boiler Feedwater Management
Because water is central to the boiler’s ability to produce steam, its level, composition and efficient use are key parameters in a power plant’s ability to operate successfully.
As steam leaves the boiler, the water needs to be replenished to avoid the losses from steam production.
The boiler has an indicator called a feedwater regulator. When the water level nears the minimum specification, feedwater is automatically added to the boiler.
The quality and temperature of the feedwater can also alter the boiler’s efficiency.
Untreated water is often too acidic and can contain dissolved solids that cause boiler tube corrosion, plugging or mechanical damage.
Minimizing scale build-up on internal and external surfaces of boiler tubes is an important part of boiler management
Imbalances in water composition are corrected by chemical treatment.
Conditioned water not only protects against corrosion, but also enables the boiler to produce higher quality steam.
Inlet water temperature greatly affects boiler efficiency. Logically, if boiler feedwater is cold it will take a longer time and use more fuel to create steam.
We discuss boiler feedwater preheating later, in the section on plant efficiency.
Thermal Power Plant – The Turbine
Let’s move on to the second step required to create electricity at a thermal power plant using a turbine, which resembles a windmill.
The plant steam turbine has groups of nozzles, vanes and blades, which are called stages.
These multiple stages form what is called the turbine rotor assembly.
High temperature, superheated, pressurized steam is directed to the nozzles in the turbine’s first stage. As the steam pushes against the blades, the entire rotor assembly turns.
Some sophisticated turbines maximize efficiency by carefully controlling the temperature and pressure drop across multiple stages – rather than all at once.
In summary, a turbine is where the steam’s thermal energy from fuel combustion is converted to rotating mechanical energy that drives the generator.
Turbines can also be divided into two types, impulse turbines and reaction turbines.
Staged Turbines
As steam moves through the turbine it loses pressure and thermal energy. It expands in volume and requires increasing diameter and longer turbine blades at each succeeding stage, to extract the remaining energy.
To leverage this phenomenon, modern thermal power plants employ a series of steam turbines connected to each other on a common shaft, called a staged turbine.
There is usually a high-pressure turbine at the front, followed by an intermediate-pressure turbine, and finally one, two, or three low-pressure turbines at the back.
When the steam pressure drops below usable levels, it’s evacuated out of the turbine as exhaust steam. More about exhaust steam treatment later.
The Generator
The final step in electricity creation is the generator.
The generator has a central shaft that is coupled tightly to the turbine’s rotor. As the turbine’s rotor and blades turn from the high pressure steam, the generator also rotates.
Inside the generator is a set of magnets and coiled wire conductors. As the generator rotates, magnet movement inside the coils induces a flow of electrons into the conducting coils.
This magnetic induction phenomenon becomes electricity and is the basic process in any generator.
Power plant generators are typically about 30 feet long and 12 feet in diameter.
The turbines are located very close to the generator to minimize any mechanical and heat losses.
Power Distribution
The generated electricity then travels to a transformer at the power plant.
Here it is “stepped-up,” or boosted to a very high voltage, because electricity loses some of its energy as it travels thorough long-distance power lines to end-use customers.
Today, huge metal towers, called pylons, carry this high-voltage electricity, along overhead cables, to locally-controlled electric grids, called substations.
Transmission power line voltage can vary between 69 kilovolts, abbreviated as KV, to 765 KV depending on distance to the substations.
Once electricity reaches a local substation, a “step-down” transformer converts it back to a lower voltage that is safe and practical for residential and commercial use. In Europe and South America the voltage standard is 220 volts, and in the US and Japan it is 120 volts.
Improving Thermal Power Plant Efficiency
The key ways to improve efficiency in a power plant are to:
- Reduce fuel consumption,
- Maximize use of heat energy available across the system, and
- Minimize water losses.
We will discuss four pieces of equipment used in most power plants to maximize efficiency:
- The Air Preheater,
- Condenser,
- Economizer, and
- Cooling Tower.
Air Preheater
A key goal is efficient combustion of the fuel. To accomplish this, the plant’s furnace controls operate a system of fans to routinely supply the correct fuel-air mixture in the boiler.
Ideally the combustion air should be heated, so an air preheater is often installed to take advantage of the heat in the rising exhaust gases, often called the flue gas.
A large source of heat energy that can be reused is the turbine exhaust. At the last turbine stage, the steam is still hot – even though it has lost most of its inlet pressure and temperature.
The Condenser
A vacuum is essential to keep a consistent steam flow through the turbine. Additionally, the turbine exhaust steam can be converted back to water, to be re-injected into the feedwater system.
Both these actions are performed by a condenser.
A condenser is composed of a large shell and tube heat exchanger. Cooling water continuously flows through the tubes, often from a nearby lake or river.
Turbine exhaust steam enters the condenser shell where it comes in direct contact with the cooler tubes.
Here the steam changes from a gas to a liquid, called condensate – clean distilled water. It is pumped back into the feedwater system.
The Economizer
Feedwater from the condenser often goes through an extra preheating step located inside the boiler known as the economizer.
Here, excess boiler heat is applied to the feedwater to raise its temperature and reduce fuel consumption.
The Cooling Tower
As the cooling water passes through the condenser, it is heated and should not be returned to its original source, as this is considered a form of thermal pollution.
A cooling tower is used to regulate the water temperature – either to be returned to the source or for recirculation in the condenser.
When the warm water reaches the top of the tower it is allowed to trickle down inside the tower, over various types of fill material, to increase the surface area for evaporation.
As it falls, the water contacts ambient air rising up through the tower either by natural draft or forced draft, using large fans.
The smoke often seen from power plants is not pollution, but steam from the cooling towers.
Flue Gas
That’s all on plant efficiency… Let’s move on.
Flue gas is the term for exhaust gas produced when a fossil fuel like coal oil or natural gas is combusted in the power plant.
Flue gas is usually composed of excess oxygen remaining from the intake combustion air, carbon dioxide, water vapor and nitrogen.
It also contains a small percentage of pollutants such as particulate matter, carbon monoxide, nitrogen oxides and sulfur oxides.
You can learn more about the way these pollutants are removed in our Flue Gas Desulfurization module.
The Stack
To evacuate the exhaust gases to the atmosphere, a flue-gas stack is used.
It is a type of chimney, a vertical pipe or similar structure.
What appear to be concrete stacks almost always employ an inner steel liner through which the flue gas is carried
Flue gas stacks are often quite tall, up to 400 M or higher, to ensure the exhaust pollutants are dispersed over a greater area.
In most countries, atmospheric dispersion models are used to determine the stack height needed to comply with local air pollution regulations.
Thermal Power Plant Summary
You must now appreciate there is more to a thermal power plant than just the boiler, turbine and generator.
Numerous pieces of equipment are also needed to and improve fuel consumption, maximize use of the heat energy and minimize water losses.
From our discussion today, you should now understand that:
A superheater raises the temperature of wet steam to 500° C, improving turbine performance.
Boilers today are closed containers with internal tubes where thermal energy converts water into pressurized steam.
The quality and temperature of the feedwater can alter the boiler’s efficiency.
As steam moves through the turbine, longer blades are needed to extract the remaining energy.
As the generator shaft rotates, magnet movement inside coiled wire induces a flow of electrons.
Electricity loses some of its energy as it travels through long-distance power lines.
The turbine exhaust is a large source of heat energy that can be reused.
Condensate is clean, distilled water pumped back into the feedwater system.
Excess boiler heat applied to the feedwater reduces fuel consumption.
A cooling tower regulates water temperature.
Flue-gas contains a small percentage of pollutants such as Sulfur Dioxide.
Stacks ensure the combustion exhaust pollution is dispersed over a great area.