Learn more with our online oil and gas courses:
Oil & Gas Drilling Fundamentals
The Drilling Fundamentals lesson consists of the following topics:
- Learning Objectives
- Lesson Themes
- Drilling: Where, What and How
- Geology
- Rocks
- Tectonic Plates
- Reservoirs
- Formations
- Stresses
- Hostile Environments
- Total Vertical Depth (TVD)
- Horizontal Wells
- Deviated Wells
- Directional Drilling
- Multilateral Wells
- Importance of Oilfield Services
- Contract Drilling
- Land Drilling Contractors
- Offshore Drilling Contractors
It is helpful to divide both the drilling and production subjects into four basic themes around the key factors that drive operations complexity, including:
- Hydrocarbon type, whether oil or gas,
- Reservoir type, whether conventional or unconventional,
- Location, whether onshore or offshore, in remote or severe climate environments, and
- Finally, the equipment. For drilling this includes the type of drilling rig and subsurface equipment.
LEARN MORE ABOUT OUR ONLINE OIL AND GAS COURSES
Drilling - Where, What, and How
The actual process of drilling a well is much the same as using a power drill to perform a workshop task.
[show_to accesslevel="premium" no_access='Sorry! This content is for Premium Members only. Sign up today!']
- Before drilling, measurements are made to show where to drill.
- The material, the size of the hole and how deep to drill will determine the proper type of drill bit
- It will also determine how big the drill motor needs to be to drive the bit in a rotary motion.
The concept of the overall drilling process is relatively simple. There is a potential reservoir located deep beneath the earth’s surface. In order to gain access and extract oil or gas, a hole must be drilled through the various rocks, materials and layers to reach it.
In oil and gas drilling, the "how" to drill the well, is the subject of this module and, is often, the last element to be considered. First, the team must define:
- Where to drill - based on the exploration and evaluation work, the geology and potential subsurface structure
- What - determined by the reservoir and strata which set the well profile, both depth and hole size
Having defined the above, the drilling engineer can develop the "how“, including:
- The optimal drilling rig
- A detailed well design and construction
- Needed operational safety and contingency planning
- The important “go” and “no-go” decision points in the operation
Geology
Geology is the study of the solid matter that constitutes the earth. This entails all underground formations:
- the soil and rocks
- the different layers of the earth’s crust
- the core
Geologists play a big part in drilling operations. Their exploration studies determine where oil and gas might be found and what type of well is best used to reach it.
In the early days of drilling, punching holes in the earth with the hope of hitting big was basically a hit and miss prospect.
Today, technology has come a long way in determining where to drill, how deep to drill, and what type of equipment will be needed to extract the oil and gas, leading to global exploration well successes in the range of 60-70%.
Rocks
The well drilling process must get through various types of rocks in the earth. Rocks are composed of mineral or organic matter, and they lay in subsurface layers or strata throughout the world.
Rocks can contain a single mineral, such as rock salt and certain limestones, or many minerals, such as granite (quartz, feldspar, mica and other minerals).
Drilling encounters three basic types of rock, each with a different characteristic that requires a different drill bit, drill speed and bit pressure to be most efficiently and safely drilled. They are:
- Igneous Rock – This type of rock is very hard (such as granite), and was once molten rock that cooled and solidified.
- Sedimentary Rock – This type of rock is found in smaller fragments and is carried by wind or water until it settles. This type of rock is somewhat easier to drill. Examples are sandstone and limestone.
- Metamorphic Rock – Is the result of an existing rock being subjected to extreme pressure and temperature, thus transforming it into metamorphic rock. Examples of this type of rock are slate and marble.
The most common rocks (sedimentary) first settle into horizontal layers called strata.They are often then deformed by movements of the earth’s crust.
Tectonic Plates
The largest movements affecting the rock strata are related to continental drift, called plate tectonics.
The outer layer of the earth’s crust is made up of seven tectonic plates which float on top of the earth’s molten core. These plates are changing position constantly, known as Continental Drift.
The moving tectonic plates have three types of boundaries: convergent or collision boundaries, divergent or spreading boundaries, and transforming boundaries. Earthquakes, volcanic activity, mountain-building, and oceanic trench formation all occur along plate boundaries.
Tectonic plates and their movement can greatly affect the drilling process if a well is located near the plate’s collision boundaries, for example the thousands of well in California, many near the San Andreas fault.
The shifting plates can quickly alter the composition of the sub-surface strata, causing drilling equipment damage and faulty reservoir readings.
Reservoirs
Reservoirs come in various shapes and sizes. The most common conventional reservoirs in the early days of the industy were sandstones.
Today carbonate reservoirs contain more than 60% of the world's remaining oil. Carbonate formations are complex, heterogeneous, with irregular flow paths and circulation traps.
Most oilfield service companies are focused on developing cutting-edge technologies to efficiently exploit complex reservoir environments.
Formations
“Formations” is a generalized term for the rock surrounding a reservoir that must be drilled through to reach the ultimate pay-zone.
Formation evaluation, refers to the volume of rock analyzed by measurements made in the borehole, usually well log or a well test. Formation evaluation helps estimate the well’s production potential and in choosing a well completion method.
Formation evaluation is done by the Geologist. By gathering pressure data and fluid samples from a formation, Geologists and Chemical Engineers can also determine the best chemical formula for the drilling fluids needed to control the well pressure and drive the cuttings to the surface.
Stresses
Rocks buried deep in the earth are not static, but are subjected to ever changing conditions. Layers of rock place tremendous vertical pressure on the wellbore and bit. Rocks to the side exert horizontal forces on the borehole.
The final sub-surface cap rock is often more compact and significantly harder to drill through. It is important to understand these stresses when trying to determine the best way to drill to a pay-zone.
Hostile Environments
Wells today are exceeding 6,000 m (20,000 feet) in depth. At these well depths, temperatures on the drill bit can exceed 450 degrees F and pressures can exceed 15,000 psi. The presence of acid gases (H2S, CO2) and chlorides make drilling a technical challenge.
It’s important to know if hostile well conditions exist while drilling so that the proper downhole components can be selected.
Safety measures must also be put in place to protect the drilling rig staff.
Two Verticle Depth (TVD)
Two key dimensions are important in well design:
- The planned end of the well, measured by the length of drill pipe required to reach the pay-zone, is called the measured depth (MD).
- The total vertical depth (TVD) is independent of the deviations and path used to get to the pay zone.
All rig systems and equipment must be designed and setup to accommodate the measured depth (MD). First and foremost, the proper rig must be selected. The key factor driving rig selection is it’s ability to turn the drill string – measured in horse power.
TVD is important because it gives the drilling engineer an idea of the pressures and temperatures that will affect the drill string and the drill bit.
Horizontal Wells
Despite the fact that most oil and gas deposits are wider than they are thick, for more than a century, vertical drilling remained the preferred method. A horizontal well is more costly, but is able to reach subsurface objectives that could not easily be reached with a vertical borehole.
Because horizontal wells can drain a larger area, fewer are needed, which means less surface infrastructure. This reduced footprint makes horizontal drilling ideal for reservoirs that are shallow, spread out, fractured or in sensitive environments.
These factors, and technological advances that have made horizontal wells commercially viable, have led to a 20-fold increase in the number of horizontal wells in the US over the past two decades.
With a vertical well a geologist’s role is primarily to evaluate “what has been drilled.” With horizontal wells geologists now become part of the drilling operation, actively involved in steering the well along a desired profile and responding to feedback data as drilling occurs.
Deviated Wells
Deviation is the angle at which a wellbore diverges from the 90° vertical position.
Most deviations occur naturally because of the flexibility of the drill string and reaction to downhole structures, such as dips in the rock beds being drilled through.
A wellbore can be deliberately deviated to miss high-risk obstacles or to reach additional reservoirs. Wells are also deviated to avoid sub-surface areas that may contain high concentrations of toxic gas.
Today, wells commonly are turned to a horizontal direction to:
- increase exposure to producing zones
- intersect a larger number of fractures
- follow a complex structure
Wells often are deviated by the use of a steering mechanism attached to the drill string.
Directional Drilling
Directional drilling is the intentional deviation of a wellbore from the path it would naturally take.
This is accomplished through the use of specialized drilling equipment such as whipstocks, mud motors, and bottomhole assembly (BHA) configurations.
Downhole instruments continuously measure the path of the wellbore in three-dimensions. Data links to the surface communicate these measurements to allow constant adjustment to the mud motors and BHA components.
The directional driller also can alter other drilling parameters such as weight on the drill bit and rotary table speed to direct the bit to the desired directional path.
Multilateral Wells
A decrease in the footprint also comes from multiple horizontal wells being drilled from the same pad. The most common method is where a driller moves the rig a few yards and starts another vertical shaft.
It is also possible to drill multiple wells from the same vertical borehole. In this technique, called multilateral drilling, two or three horizontal boreholes, each a few hundred to a few thousand feet long, can be drilled from the same main stem, like the branches of a tree or a candelabra. This technique is especially common offshore or in environmentally sensitive onshore locations.
Multilateral drilling creates a highly productive drainage network in reservoirs with many isolated pockets of oil or gas.
Advances in multilateral drilling and completion technology promise reduced well costs, greater flexibility and increased profit potential for the operator.
The TAML (Technical Advancement of Multilaterals) joint-industry project was formed in 1997 to educate the industry on the advantages of multilateral wells.
Multilaterals have proven successful in various drilling- production applications, but members of TAML feel that the industry still does not recognize the full potential of the technology.
Some estimate that 10% of the 60,000-70,000 oil and gas wells annually drilled worldwide are multilateral candidates, while TAML places the percentage as high as 75%.
Oilfield Services
As the chart from the Independent Petroleum Association of America (IPAA) indicates for a typical US well drilled in 2003-2004:
- Drilling rigs are about 30% of well cost
- High quality steel OCTG (Oil Country Tubular Goods) are another large cost factor, at about 14% of well cost. They are provided by global steel manufacturers.
- As a group, technical services including cementing, drilling mud, formation treating and well testing account for another 19% of well cost.
- The largest remaining miscellaneous category (at 20% of well cost) includes roustabouts, equipment, pipe inspection, materials and supplies to the rig, casing crews, etc.
Note that these percentages are directional only. Well cost, especially price per foot, varies with area and reservoir structures etc. Directional drilling and multiple fracturing treatments add to the cost in many locations. Considered a fixed cost, rig cost is a higher percentage on a shallow well.
Recently, costs for all goods and services have been on the rise because of tight supplies.
Contract Drilling
Today, most of the global drilling rig fleet is owned by contract drilling companies.
Typically, a term contract is entered into between the E&P operator and the contract driller. The rig services provided to E&P operators include experienced personnel and specialized equipment.
Drilling contracts can be a mixture of types, depending on:
- the general E&P expenditure business cycle
- the type of market for the rig, I.e., US vs. foreign location and e.g. onshore vs. offshore
- rig availability due to new construction and those currently under contract
Land Drilling Contractors
The drilling rig - provided by a contractor- is the largest single cost of drilling a well. Based on revenue, drilling rig contractors are the largest segment of the Oilfield Service industry.
All onshore wells are drilled from the surface using a land rig. Land rigs can also be jackknife and helicopter rigs, which can be broken down into small enough pieces to be transported to a remote land location by truck or helicopter. The onshore rig industry tends to be a localized industry, because the cost of moving the rigs regionally or internationally can be high.
High oil prices make it profitable to explore and to redevelop old fields, generating activity for light workover rigs and coiled tubing drilling (CTD) systems.
In the US, the new rush toward drilling deep shale gas plays will require higher powered rigs (1,500-hp and higher). These wells are one of the highest cost options in a E&P operator’s plan. If natural gas prices become depressed, drilling these wells could be curtailed.
Offshore Drilling Contractors
Offshore rigs are massive, self-propelled, semi-submersible rigs and drill ships designed to work in thousands of feet of water.
The market for offshore oil and gas drilling services continues to expand and new builds swell the fleets.
As of mid 2008, more than 90% of the world’s mobile offshore drilling units were under contract, according to the Oil & Gas Journal.
In addition to exploration wells, operators have committed large amounts of capital to drill and develop major projects around the world. Some analysts say that these new projects will go forward with crude oil prices in the $50-60 range.
Offshore drilling rig contracts are now lengthening to almost 2 years, in response to:
- increasing demand
- reduced rig availability
- long lead times for new construction because of manufacturing and equipment bottlenecks
[/show_to]
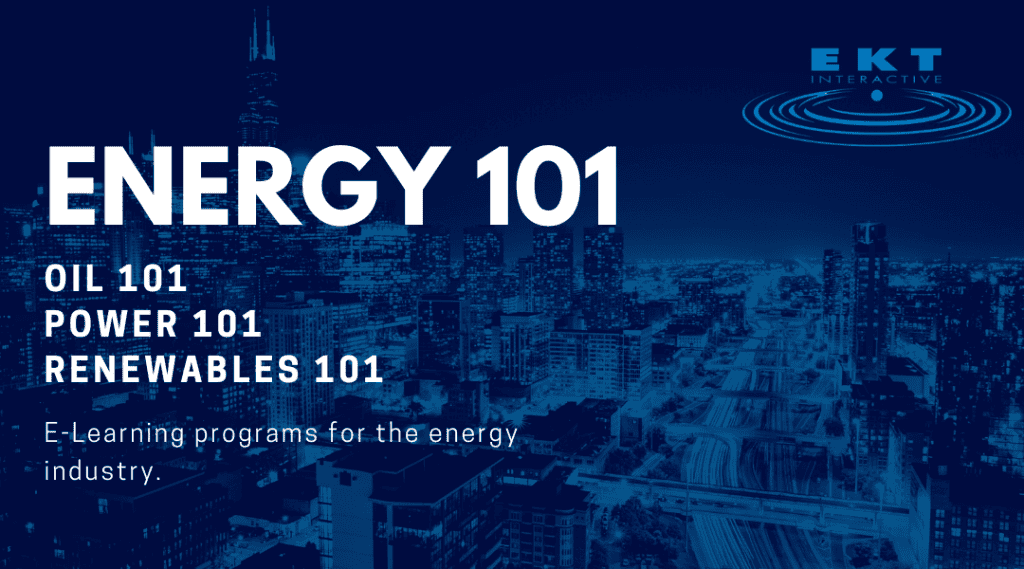
Whether it’s oil and gas, power, or renewables that is your chosen career path, our e-learning courses can help you get a leg up on the competition and get your food in the door.
We often hear from learners who successfully use our courses to prepare for the interview process. After all, you’re using the same courses that companies themselves use to prepare their teams.
As this student passed on:
I would like to thank you for your brilliant Oil 101 materials. I did use it to prepare for the recruitment process, and managed to take a new role in the oil and gas industry!
Get started with our Energy 101 courses today!
Related Resources
Energy Risk Management
Risk Management in Oil and Gas
Oil 101
Power 101
What is a Nuclear Power Reactor Operator
Watts, Kilowatts, Megawatts, Gigawatts
Jobs Data
Global Energy Talent Index (GETI)
US Energy & Employment and Jobs Report (USEER)
Career Path in Energy Articles
Is Oilfield Services/Equipment a Good Career Path
Is Oil and Gas Production a Good Career Path
Is Electric Utilities a Good Career Path
Is Power Generation a Good Career Path
Hydrogen and the Hydrogen Economy