Introduction to Gas-Fired Power Plants
Power generation is one of the largest and growing industrial uses of natural gas. It’s clean burning and has lower carbon dioxide emissions than coal.
Natural gas has often been called the bridging fuel to a carbon-free energy environment.
Shale gas developments around the world will transform global power applications for natural gas, especially as liquefied natural gas markets mature.
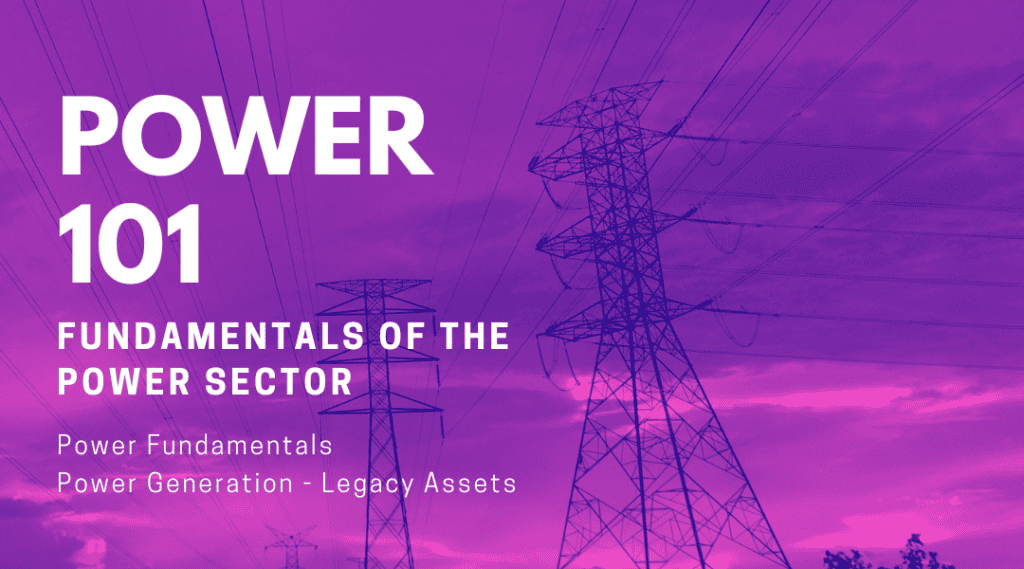
Power 101 – Learn more with our Power 101 eLearning course
Overview
This lesson presents the specific types, equipment and operating conditions of natural gas-fired power plants.
It includes the following topics:
A thermal power plant analysis framework.
Operation of a gas turbine engine, the prime mover in a gas-fired plant.
How natural gas gets to a power plant.
The two types of natural gas-fired plants:
Open-cycle and
Combined-cycle.
The importance of the Heat Recovery Steam Generator and
Heat exchangers, the
Diverter damper and
Acoustic equipment.
Controls.
A Thermal Plant Analysis Framework
Let’s first introduce a framework to help evaluate any thermal power plant.
The essence of the power generation process is fuel conversion to energy using two types of systems.
The primary system is often called the fuel-air system or the fireside of the plant.
It is fuel-specific and for a natural gas-fired power plant includes:
gas production and treatment,
compression, pipeline transportation and storage.
local distribution entities, and
combustion in a gas turbine engine.
The secondary system is the water-steam system – often called the waterside of the plant. The presence of a waterside depends on the type of gas-fired power plant.
In an open-cycle power plant, the gas turbine prime mover is coupled directly to the generator, so there is no waterside equipment.
On the other hand, in a combined-cycle power plant, a large piece of equipment called the Heat Recovery Steam Generator converts the exhaust heat energy from the gas turbine to steam.
The produced steam is expanded through the power turbine – which drives a generator – creating power to the grid…. a similar waterside operation to a coal-fired power plant.
Gas Turbine Basics
Before going into detail on the operation of a gas-fired plant, let’s get familiar with a key plant component – the gas turbine engine.
Gas turbines play an important role in the lives of many people.
Related Topic: What is Natural Gas?
They power airplanes; and it is reported that over 200,000 people pass through some of the world’s largest airports every day.
The aviation industry calls their gas turbines – jet engines – and three components are common to every design:
- First, air is compressed by a rotating set of vanes and blades.
- Then, a combustor adds fuel, to heat and expand the compressed air.
- Finally, a turbine extracts power from the hot air flow.
The aircraft jet engine provides enough power to both turn the compressor and generate the thrust energy needed to make the plane fly.
The electric utility industry generally calls this equipment an industrial gas turbine.
As you can guess power plant gas turbines are much larger than those in airplanes. Some power plant gas turbines can weigh 40 tons!
The industrial gas turbine has application advantages, including:
- A high ratio of power, relative to its size and weight.
- Low maintenance cost and a long mechanical life.
- Wide fuel flexibility, light distillates for aircraft and natural gas for power.
Operational advantages include:
- Startup time to full load is measured in minutes vs. hours for a steam turbine plant, and
- Higher thermal efficiencies than for most steam power plants.
Natural Gas Fuel Management
Before we learn about the plant equipment, let’s discuss natural gas supply. It starts at a typical oil & gas field. Here production from numerous wells is collected via a gathering system and moved to a treatment facility.
Unlike the fuel management system for coal where everything is above the surface, natural gas movements are hidden.
At the wellsite all liquids are separated, and any wellhead contaminants are removed, including: sulfur, nitrogen, hydrogen sulfide, carbon dioxide and water.
Natural gas must meet specific quality measures before entering the gas pipeline network.
Natural gas is then compressed to be moved by pipeline hundreds or even thousands of miles, using large compressor stations, both in the field and along the pipeline.
Long-distance pipelines can be 24 to 36 inches in diameter because they move billions of cubic feet every day, abbreviated as BCFD.
Natural gas pipelines are buried in what is called a right-of-way to minimize the long term impact on the environment and maximize safety.
At the receiving end, natural gas moves to what is called a Distribution Network Operator, or DNO; known in the US as a Local Distribution Company, or LDC.
They provide a series of small-diameter pipelines, called mains, to service homes, power plants and large industrial customers.
Natural gas supplied to any industrial customer requires the DNO or LDC to maintain consistent and adequate pressure in the system.
Demand for natural gas fluctuates both daily and seasonally, while field production is relatively constant in the short term.
To manage fluctuations, natural gas is often stored in large volumes in underground caverns.
Storage of natural gas during low-demand periods helps ensure that consistent supplies are available during high-demand periods.
Energy 101 – Online Training Courses, from Oil and Gas to Power and Renewables
Two Major Natural Gas Pipeline Systems
European Natural Gas Pipelines
Gas pipeline networks are huge, and let’s discuss just two examples.
Europe is supplied primarily by Gazprom.
The Russian national company owns the world’s largest gas transmission system of 172,000 kilometers.
Gazprom also has major expansions underway to move more Russian gas to Europe and China.
US Natural Gas Pipelines
In the US, residential and industrial customers are supplied by over 500,000 kilometres of mainline transmission pipelines, owned by private companies, but regulated by the Department of Energy.
There are also numerous projects underway to expand US gas pipeline capacity — thanks to the success of shale gas developments.
A Word about LNG
Note that natural gas can also be stored and shipped as a liquid. LNG is simply natural gas in liquid form.
At a receiving location, the LNG is converted back to natural gas by a process of regasification – ready for use at a gas-fired power plant.
You can find out more about LNG in the Oil and Gas 201 module.
The Open-Cycle Power Plant
Now that you understand how natural gas gets to the plant, let’s begin with a discussion of an open-cycle power plant, which uses an industrial gas turbine, mechanically coupled to a generator.
This plant type has only one power cycle.
The natural gas chemical energy is converted directly into mechanical energy to turn the generator at approximately 3,000 RPM.
There is no provision to recover the energy in the power turbine exhaust, which can range between 500 and 600 degrees Celsius.
Open-cycle units are often used in oil and gas field operations for power and mechanical drives, utilizing the excess gas available at the wellsite.
Open-cycle power plants can quickly reach full power and are easy to shut down — with little impact on the mechanical equipment.
Therefore, they are ideal as peak shaving power plants, which can operate from several hours per day to a couple of dozen hours per year, depending on the electricity demand and the generating capacity of the grid.
A typical open-cycle plant may produce 100 to 300 megawatts.
Today, the top units have a thermal efficiency in the range of 42%, up from 35% in the 1990s.
The Combined-Cycle Power Plant
A combined-cycle power plant, or CCPP, is an assembly of natural gas and steam turbines that work in tandem to recover the maximum amount of heat energy, converting it into steam to drive single or multiple generators.
Since the power turbine exhaust gas is hot, a subsequent steam turbine can extract additional energy.
Each CCPP power-generating system consists of an industrial gas turbine, a Heat Recovery Steam Generator, or HRSG, a steam turbine, controls and a separate generator.
We will discuss the HRSG in more detail shortly.
A combined-cycle power plant can produce up to 50% more power than an open-cycle plant.
The International Energy Agency reported that combined-cycle plants accounted for roughly three-quarters of global plant capacity additions in 2015. The Middle East, China and the US were responsible for over half of the investment activity.
Combined-cycle power stations are made up of one or more gas turbines. Each has an HRSG arranged to supply steam to a single or multiple steam turbines in what is called a cycle block.
In 2014, Japan had three of the world’s largest natural gas-fired power plants, all running on LNG. Each station was designed with numerous CCPP cycle blocks, each in the range of 500-700 megawatts.
There are large and increasing quantities of natural gas available around the world thanks to LNG movements. Combined-cycle plants are now being developed for what is called continuous or “baseload power.”
A baseload plant has a limited range of load variability which is determined by the quantity of electricity needed on the grid, despite the time of day.
Historically, baseload plants were either coal or nuclear powered. So this is quite a shift.
State-of-the-art combined-cycle gas turbine plant efficiency now exceeds 60%, with expected improvement to 65% over the next decade.
Combined-Cycle Power Plant Components
HRSG Basics
As was mentioned earlier, power turbine exhaust temperatures of 500 to 600°C are well suited to efficient combined-cycle operations.
The major piece of equipment used in a combined-cycle plant is the HRSG. It is an efficient series of heat exchangers that:
recovers heat energy from the exhaust gas stream, and then
produces superheated steam to drive turbines to generate electricity.
HRSGs are huge and are built as modular units to give them flexibility in both construction and application.
As you will see, the gas side of the HRSG operation begins at the discharge of the power turbine and flows in a single pass through various HRSG modules. The cooled gas escapes to atmosphere through the stack.
The waterside operation starts with the economizer and then flows across the HRSG modules to finally generate superheated steam, which is then routed to steam turbines.
HRSG Equipment
Now let’s look at the HRSG equipment components in more detail … starting with the economizer that recovers the last bit of energy in the power turbine exhaust stream.
It increases the temperature of feed and recycle water before it enters the evaporator… a similar operation to feedwater pre-heaters in a coal-fired plant.
Moving to the evaporator, in this section the boiling process and steam generation occurs. The evaporator is similar in design to the boiler in a coal-fired plant, and has a mixture of steam and water in its internals.
The function of the superheater is to increase steam temperature above its saturation point. As you know, high steam temperatures improve cycle efficiency.
The superheater sections typically have the highest metal temperatures in the HRSG.
Finally, duct burners use supplementary natural gas firing to increase the heat energy of the gas turbine exhaust, making it possible to increase the output of the HRSG.
Power Plant Heat Exchangers
Maximizing heat transfer is a key objective to improve power plant efficiency, and two types of heat exchangers are commonly used:
Finned tube exchangers, and
Shell and tube exchangers.
Finned Tube Exchangers
The finned tube design is more efficient when one side of the exchanger is vapor or air, and a fluid is carried in the tubes.
In the HRSG, the superheater and economizer use a finned tube design.
Shell and Tube Exchangers
As mentioned in the introduction, the waterside operation of a combined-cycle power plant is the same as the steam cycle in a coal-fired plant.
In a similar way, shell and tube heat exchangers are used as condensers to convert the steam turbine exhaust back to water to be recycled through the HRSG economizer.
Shell and tube exchangers are ideal in fluid-to-fluid heat transfer applications.
The Diverter Damper
A combined-cycle plant is also equipped with a diverter damper.
The diverter damper is a set of large-diameter ductwork, valves and a stack that direct the power turbine exhaust to flow to either the:
- HRSG for combined-cycle operation, or a
- Bypass stack for open-cycle operation.
Construction of a new combined-cycle power plant is measured in years – not months.
Typically, the utility will choose to complete the project in phases where:
- Phase 1 is to install the gas turbines and generators in open-cycle mode – to sell power to the grid while the combined-cycle facilities are still under construction.
- Phase 2 brings the HRSGs and the steam turbines online.
The diverter damper allows for the rapid configuration of the power plant either as a combined-cycle or open-cycle system.
It also allows the plant to be operated in open-cycle mode when HRSG or steam turbine maintenance is required.
Acoustic Packages
All thermal power plant equipment has a strong noise impact on the surrounding area.
Remember, in a gas-fired power plant there is a jet engine sitting inside a building!
On the plant floor, operating staff must have protection from significant noise levels generated by the turbines, generators, the air intake and the turbine exhaust.
Acoustic mitigation is an integral aspect of any new development or plant expansion. There are numerous respected global acoustic expert consulting firms that are engaged by the contractor at the early stage of plant design.
A variety of silencer types are used at thermal power plants, including:
Mufflers – Used on the exhaust of smaller gas turbine installations.
Air Duct Silencers – Applied in most airflow applications.
Sound Enclosures – The engine manufacturer often provides the gas turbine with a protective thermal wrapping or an enclosing cabinet.
Acoustic Louvers – Provides sound reduction in the building, without restricting airflow to the equipment.
Acoustic enclosures for a gas-fired turbine installation must also give weather and fire protection.
Gas-Fired Power Plant Controls
Now, a quick word about plant operation controls.
Like a coal-fired plant the major control task is to regulate the plant’s electrical power output to meet a variable demand on the grid.
In a gas-fired plant, there are three major control areas:
Gas turbine engine performance,
Startup and shutdown operations, and
Steam and airflow management in combined-cycle plants.
The first measurement is the quality and humidity of the inlet air, which has a major impact on gas turbine performance.
Then, operating parameters such as temperature and pressure in the compressor and power turbine are managed in real time.
Finally, the exhaust gas temperature and pressure is monitored.
Power turbine speed is also carefully monitored because in an open-cycle operation, the power turbine is coupled directly to the generator.
Open-cycle power plants operate in a wide variety of peak power modes.
To routinely manage this variability, sophisticated control systems are put in place to start, run and shutdown the individual components in the plant.
Note that any gas turbine compressor does not supply enough air to be self-sustaining until it reaches approximately 60 per cent of its rated speed.
In larger machines, the generator can also be controlled as a synchronous motor to get the compressor to needed speed.
Then, it shifts back to generating once the system stabilizes.
In combined-cycle plants, the control system must manage:
large volumes of power turbine exhaust air,
the quality of the steam generated in the HRSG, and
steam turbine performance.
These control systems are very sophisticated to integrate the operation of all of the plant’s equipment, beyond the gas turbines, to create an economical and stable power generating facility.
Combined Cycle Technology
Combined cycle technology enables power plants to generate 50% more electricity from its fuel, than it would with a conventional open cycle power system.
Under this dual phase system, two combustion turbine generators operate in conjunction with two heat recovery steam generators and a steam turbine generator.
In the first cycle, fuel is burned and the resulting combustion gases power two turbine generators to produce electricity.
Hot exhaust, normally lost during this process, is captured and routed through the two heat recovery steam generators.
These units boil water to create steam, which spins an additional turbine generator and produces more electricity.
Finally, the steam is discharged into a condenser which returns the steam to its liquid state for recycling.
Gas-fired Power Plant Summary
You should now have a good idea of the operation and types of equipment in a gas-fired power plant.
Note that in 2015 combined-cycle plants accounted for roughly three-quarters of plant additions.
The main obstacle to more gas-fired power plants in developing countries is the lack of pipeline networks needed to take advantage of available and economic LNG shipments.
From our discussion today, you should now understand that:
Power generation is one of the largest and growing industrial uses of natural gas. It’s clean burning, and has lower carbon dioxide emissions than coal.
An industrial gas turbine is very similar in operation to an aircraft jet engine, with a compressor, combustor and power turbine.
A DNO or LDC is the regulated utility responsible to provide natural gas to power plants within a specific metropolitan region.
Though pipelines are the primary mode of gas transportation, LNG is becoming a “virtual pipeline” to move large, economic quantities of natural gas around the world.
The combined-cycle power plant produces up to 50% more power than an open-cycle plant, by harnessing the gas turbine exhaust to power a steam turbine.
Baseload power plants provide consistent electricity to the grid; whereas peaking plants operate only during peak times of energy demand.
In a combined-cycle plant, the Heat Recovery Steam Generator produces steam for a separate steam turbine and generator set, to get another level of power from the plant.
There are two types of heat exchangers in a gas-fired power plant: finned-tube and shell-and-tube.
A diverter damper system is needed to manage the high volumes of hot exhaust gas in a combined-cycle plant, because they are often built in phases.
Sophisticated acoustic packages are designed to muffle the noise emitted from power plants.
The control system for an open-cycle power plant must address numerous short-cycle startup and shutdown operations.